
Frequently Asked Questions
What to know before you get started:
Consider what matters most: the upfront cost of the blade or the expense per cut. If you're tackling small tasks or only using it occasionally, opting for a cheaper blade might make sense. However, for larger projects or frequent use, investing in a higher-priced blade can prove more economical over time as it typically offers a lower cost per cut. In the case of substantial projects, prioritizing the lowest sawing cost per foot often outweighs the initial price consideration.
Correctly identify what you’re cutting:
The paramount consideration when selecting a diamond saw blade is accurately identifying the material you intend to cut. This crucial factor directly impacts both cutting speed and blade longevity. To achieve optimal performance—maximizing cutting speed and extending the blade's lifespan—the material should closely match the blade. As a rule of thumb, prioritize identifying the material you'll cut most frequently or for which superior blade performance is paramount.
Choosing wet or dry cutting:
The choice between wet or dry cutting methods may hinge on personal preference or specific job requirements. When operating electric hand tools and saws, water isn't safe due to the electrical power source. However, for concrete saws, wet cutting is typically favored because water serves as a coolant, enabling deeper cuts. In the case of tile and masonry saws, both wet and dry cutting blades are viable options. Dry blades are more commonly used with power cutters, yet they are often employed with water to manage dust. It's crucial to note that wet blades necessitate the use of water, whereas dry blades can be utilized either dry or wet, depending on the task or equipment specifications.
The significance of segment height:
The total segment heights of diamond blades might not give an accurate picture due to the presence of non-diamond bearing segment bases essential for laser welding or brazing.
Relying solely on diamond blade segment height isn't indicative of the blade's actual worth. Various factors influence its performance and overall value. These include diamond size, concentration, and quality, as well as the bond hardness, cutting power (torque) of the saw, and how well the blade specifications align with the material being cut.
Keeping Your Diamond Blade Cool to Extend Its Life and
Improve Its Performance:
Dry cutting diamond blades offer the convenience of usage without the need for water tanks, hoses, or wet slurry clean-up. These blades rely on airflow around them to prevent excessive heat buildup during cutting.
For "intermittent" sawing, dry diamond blades are recommended. It's advised to release pressure from the blade after every 10 to 15 seconds of cutting, allowing it to return to full speed for several seconds. This "cooling" interval facilitates air circulation around the blade, dissipating heat. Dry diamond blades are versatile, performing well both dry and wet, depending on the job or equipment requirements. However, wet cutting diamond blades necessitate the use of water to prevent excessive heat buildup during cutting. Water usage also helps minimize dust.
Why won’t my block or asphalt blade cut hard brick or concrete?
Block and asphalt are highly abrasive materials, requiring diamond blades with an exceptionally hard bond. Conversely, for brick or hard concrete, a blade with a softer bond is necessary to ensure proper wear in materials with higher P.S.I. and lower abrasiveness. If a blade is too hard, it won't wear correctly, it will fail to expose new diamonds, and eventually cease cutting. Matching the blade's bond hardness to the material being cut is crucial for optimal performance and longevity.
Why shouldn’t I use my brick or concrete blade to cut block or asphalt?
Brick and hard concrete pose challenges for cutting due to their hardness and low abrasiveness. Therefore, blades intended for these materials require a softer bond. Using a softer bonded blade on highly abrasive materials can be detrimental as it causes significant wear to the soft metals in the blade. This leads to premature release of exposed diamonds and ultimately shortens the lifespan of the diamond blade. Matching the blade's bond hardness to the specific material being cut is essential to avoid premature wear and maximize blade longevity.
What makes a blade stop cutting?
The primary reason for a blade's failure to cut is typically misapplication. A decrease in cutting speed is commonly observed when working with harder materials that lack abrasiveness. When a hard bonded blade is utilized on such hard materials, it fails to wear properly. This inability to wear away at a sufficient rate results in insufficient diamond exposure, hindering the blade's ability to continue cutting through the hard material effectively. Matching the blade's bond hardness to the material being cut is essential to ensure optimal cutting performance and longevity.
What is the difference between a wet blade and a dry blade?
The primary distinction lies in how the diamond matrix is affixed to the core. Wet blades typically utilize brazing, whereas dry blades are typically laser welded. Laser welding boasts a higher melting point compared to brazing. Additionally, the bond is another point of differentiation. Dry blades commonly feature a slightly softer bond, facilitating easier cutting without the need for water to cool and lubricate the cut.
Dry Blade Definitions
Dry Blade
Any blade capable of both wet and dry use, operating efficiently without requiring water, typically utilized on high-speed saws such as table saws, handheld devices, or low-horsepower walk-behind saws.
High Speed Dry Blade:
A high-speed dry blade is any blade designed to operate on a 5200 RPM handheld saw.
High Speed Specialty Dry Blade:
Any blade designed to cut materials beyond just concrete, encompassing masonry blades or stone blades, asphalt blades, green concrete blades suitable for use on high-speed saws.
Early Entry Dry Blade:
Typically employed for cutting initial joint on green concrete, this blade can also be utilized in dry conditions, often on the same day.
Low Horsepower Walk Behind Dry Blade:
The blade size can range from 14 inches to 20 inches, compatible with low horsepower saws. A High-Speed Dry Blade can handle up to 20 horsepower, depending on the specific blade. Typically, 18 horsepower is considered safest.
Metal Specialty Dry Blade:
A vacuum brazed diamond blade offers exceptional durability, outlasting traditional abrasives without experiencing shrinkage. These blades feature a steel core with diamonds vacuum brazed directly onto it, eliminating the need for segments. Their design prioritizes safety and longevity, providing a significantly longer lifespan compared to standard abrasive fiber discs.
Rescue Dry Blade:
The rescue blade, with its 0.250-inch thickness, is a popular choice for the Jaws of Life. It's versatile enough to be utilized for various tasks, including cutting tree roots. Equipped with tungsten segments, it's specifically designed for demolition purposes, capable of cutting through metal and other obstacles encountered during rescue operations.
Abrasive Dry Blade:
The Triple-Reinforced Fiber Blade is specifically designed for cutting metal. These disposable blades are commonly purchased in packs of 10, with larger companies sometimes acquiring hundreds at a time, depending on the contractor's preference. Serving as a versatile and general-purpose metal blade, they find application in various scenarios such as stainless steel cutting, welding situations, guardrail work, or any other metal cutting tasks where a vacuum brazed diamond blade isn't preferred.
Cup Wheels (Grinders):
Depending on the cup style chosen, the grinding results can range from aggressive to achieving the desired finish as per the contractor's preference. These wheels are primarily used for grinding down high spots in concrete or for material removal, such as epoxy, to expose the aggregate. They come in various styles including single row, double row, turbo, arrow cup, etc., each serving different purposes. While cup wheels might not provide a polished finish, they do offer a finer finish. For instance, a single row cup wheel tends to leave horseshoe marks but is efficient for quickly exposing aggregate and leveling concrete by eliminating high spots. On the other hand, if a slightly nicer appearance is desired without compromising the levelness of the concrete, a turbo cup wheel may be more suitable, making it ideal for applications like garage or basement floors.
Small Diameter Dry Blade:
Small diameter blades typically range from 4 inches to 9 inches, allowing them to be used on handheld grinders without needing to remove the guard. Depending on the size of the grinder, these blades can cut a variety of materials including masonry, stone, concrete, and more.
Wet Blade Definitions
Wet Blade:
Wet blades are meticulously crafted for specific aggregates and are operated with water as a coolant. They are commonly employed on walk-behind saws ranging from 22hp to 110hp, accommodating blade diameters from 14 inches to 60 inches. These saws are equipped with water tubes that evenly spray water onto the blade and into the cut. Water plays a crucial role in maintaining the blade's temperature, preventing tension loss, core cracks, and segment detachment, thereby averting potential damage and safety hazards. Moreover, water aids in suppressing and controlling unwanted silicone dust.
Cured Concrete Wet Blade:
The Pro Series Cured Wet Blades are specifically engineered for cutting cured concrete, reinforced concrete, and hard rock. These blades are crafted using top-quality synthetic diamonds and powders to ensure faster cutting, extended blade life, and effective heat dissipation caused by friction. It's essential to understand that not all concrete blades are created equal; numerous factors are considered in manufacturing the optimal blade for specific cutting applications.
To provide the best possible product, several questions must be addressed, including the horsepower of the saw, whether it's diesel or electric, the aggregate composition, the age of the concrete, the amount of rebar (reinforced steel) present, and the location where the blade will be used. This critical information ensures the selection of the most suitable Pro Series blade for the task at hand.
Pro Series cured concrete blades are commonly paired with walk-behind diesel saws ranging from 35hp to 110hp. Blade sizes vary from 14 inches to as large as 60 inches in diameter, catering to a wide range of cutting needs.
Overlay Wet Blade:
The Pro Series Overlay Wet Blades are specially engineered for cutting asphalt over concrete, commonly referred to as "Overlay" in the industry. These blades are crafted using premium synthetic diamonds and powders to ensure quicker cutting, prolonged blade life, and effective heat dissipation caused by friction. It's important to note that not all overlay blades are created equal; numerous factors are considered in manufacturing the optimal blade for specific cutting applications.
To deliver the best possible product, several questions must be addressed, including the horsepower of the saw, whether it's diesel or electric, the aggregate composition, the age of the concrete, the amount of rebar present, the thickness of the asphalt overlay, and the location where the blade will be used. This crucial information ensures the selection of the most suitable Pro Series blade for the task at hand.
Pro Series overlay blades are commonly paired with walk-behind diesel saws ranging from 35hp to 110hp. Blade sizes vary from 20 inches to as large as 36 inches in diameter, catering to a wide range of cutting needs.
Asphalt Wet Blade:
The Pro Series Asphalt Wet Blades are specifically designed for cutting straight asphalt surfaces. These blades are crafted using premium synthetic diamonds and powders to ensure enhanced cutting speed, extended blade lifespan, and effective heat dissipation caused by friction. To ensure the best product performance, certain crucial information is required, such as the horsepower of the saw, the presence of concrete beneath the asphalt, and if so, the thickness of the concrete layer.
Pro Series asphalt blades are commonly utilized with walk-behind diesel saws ranging from 35hp to 74hp. The blade sizes range from 14 inches to 36 inches in diameter, catering to various cutting requirements.
Green Concrete Wet Blade:
The Pro Series Green Concrete Wet Blades are engineered for cutting concrete that has been poured within a 12 -24 hour period, known as green concrete. Green concrete may contain various aggregates such as flint, quartz, granite, basalt, river gravel, and limestone. These blades are meticulously manufactured using top-quality synthetic diamonds and powders to ensure faster cutting, extended blade life, reduced spalling, and effective heat dissipation caused by friction. To ensure optimal product performance, important information such as the horsepower of the saw, type of aggregate, and timing of cutting after concrete pouring is crucial.
Pro Series green concrete blades are commonly utilized with walk-behind diesel saws ranging from 35hp to 74hp. The blade sizes range from 14 inches to 18 inches in diameter, catering to various cutting needs.
Hydraulic Hand saw and Wall Saw Blade:
The Pro Series Hydraulic Blades are specifically engineered for cutting walls and floors both vertically and horizontally. Hand saw blades are available in diameters of 20”,24”,and 30” with thickness options including .125” (1/8), .140” or .145”, and .250” (1/4”). These blades offer an excellent solution for cutting tight 90-degree corners and curb cutting. They are primarily used with hydraulic hand saws operating between 5-8 GPM (gallons per minute), featuring an arbor size of 1” and a flange with 6 flush-faced bolt holes that enable flush cutting, for a flush cut saw.
Hydraulic hand saws can be equipped with an upright handle to alleviate stress on the operator's knees and back when cutting floors, sidewalks, or other ground-level work. Pro Series wall saw blades, on the other hand, are commonly used with hydraulic and high-cycle equipment for larger projects such as window openings, doorways, and walls. These blades are available in diameters ranging from 24” to 48”, and offered in various thicknesses including .187”, .220”, and .250”. Wall saw blades are typically used with track systems fixed to the wall, enabling remote and safe operation by the operator. This combination of wall saw blades and track systems is predominantly utilized by professional saw cutters.
Ring Saw Blades:
Ring saw blades offer an excellent cutting alternative for sawing through block and concrete walls. They feature a unique design, are lightweight, and are available in several sizes, including 14”, 16”, and 20” diameters. These blades are used with lightweight handheld saws, which come in various variants such as electric, gas, and hydraulic for larger workloads. Regardless of the saw model used, ring saw blades must be operated with water.
Ring saw blades provide several advantages over traditional diamond blades. These include the elimination of overcuts on corners, 2-3 times faster cutting speed, the ability to cut up to 16” deep, and reducing fatigue on the operator. However, one drawback to consider when purchasing a ring saw is the cost. Ring saw blades, coupled with the saw itself, can cost up to 2-3 times more than standard saw packages, depending on the model chosen.
Bevel Blade:
Bevel wet blades are employed in pairs, with each blade featuring a 45-degree angle, resulting in a 90-degree joint bevel in the cut. They are available in two sizes: 8” and 12” diameter, with optional thicknesses of .250”, .375”, and .500”. When paired together, the overall thickness will be 1/2”, 3/4”, and 1”.
​
These blades are primarily used in concrete applications and require water as a blade coolant. They are commonly utilized with spacers, which are supplied upon the customer's request, to ensure precise and consistent cuts.
Looping Blade:
Loop blades are meticulously engineered for cutting wide joints to accommodate the installation of electric wire for activating traffic signals. These blades are available in two different bonds tailored for either asphalt or concrete cutting applications, and they require water for operation. Loop blades come in sizes ranging from 12”, 14”, to 18”, providing versatility for various project requirements. Additionally, they offer a range of thickness options, including .250”, .310”, .375”, and .500”, allowing for precise customization based on specific cutting needs.
Refractory Blade:
Refractory blades are purpose-built for cutting industrial firebrick and are available in various bonds and sizes to suit different needs. Common sizes include 14”, 18”, and 20”. Some refractory blades are equipped with silent core technology, aimed at reducing noise levels to improve work conditions and meet OSHA noise regulations. These blades find applications not only in cutting firebrick but also in constructing rotary kilns, chimneys, industrial furnaces, and flu linings. Refractory blades are typically utilized with wet cutting table saws for optimal performance and longevity.
Diamond Beaded Wire:
Diamond wire finds extensive use in various industrial applications, including offshore sawing, bridges, concrete walls, stone cutting, jetties, columns, pipes, and large-scale projects that surpass the capacities of conventional diamond tools. One of its significant advantages is its versatility, as it can be assembled on-site using a crimping tool to tailor the wire to the specific size required for each project. This flexibility is crucial since the wire operates with a pulley system, and sizes may vary from one project to another.
Different pulley systems are available, including high-cycle, hydraulic, hydro stress, and electric, with optional water spray for cooling purposes. These pulley systems can be remotely operated from a distance using a control unit and cables.
Diamond wire comes in several thicknesses ranging from 8mm to 13mm and is manufactured using various diamond matrix types, including sintered, vacuum brazed, and electroplated. The wire is produced in three bead shapes: cylindrical, conical, and bi-conical. Cylindrical wire, typically 10.2mm in diameter, is commonly used for pipe cutting and can operate bi-directionally. Bi-conical wire, also typically 10.2mm in diameter, is primarily used in electroplated form and can operate bi-directionally, suitable for pipe cutting applications as well. Conical wire, available only in electroplated form, has limited use and must be used in one-directional sawing.
The choice of wire aggregate varies depending on the wire type: stone and concrete are common aggregates for electroplated wire, while stone, concrete, and steel are common aggregates for vacuum brazed wire. Sintered wire is commonly used for reinforced concrete and stone cutting applications.
Haven't found what you're looking for?
Please contact us at 888-281-3010 or info@nsdiamondsolutions.com.
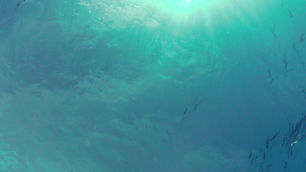